温总理在“政府工作报告”中提出了“今年单位国内生产总值能耗降低4%左右”的节能宏观调控目标,从而将节能提至前所未有高度。对电机行业来讲,量大而广的中小电机,其所消耗的电能约占全国发电量的60~70%,是最大的耗能大户,因此中小电机的节能是电机行业面临的严峻课题,也是电机行业发展的新机遇。
一 中小型异步电动机行业的现状和发展趋势
现状
(1)目前中小型电机产量较高的省市依次为山东、江苏、河北、上海、浙江、广东和辽宁,可见企业大多集中在沿海地区。
(2)由于新兴的民营企业以及合资、外资企业的发展,使中小型电机行业中,国有企业的比重下降,而且中小型电机的产量逐步向“生产大户”集中。
(3)中小型电动机已完整地建立了三相异步电动机Y、Y2、Y3系列。
1985年迅速推广了Y系列及其派生系列产品,其功率范围为0.55~250KW,机座中心高为80~315。 通过引进消化美国西屋公司和瑞士BBC公司的技术,自行研发的Y系列6KV、220~2800KW中型高压三相异步电动机,采用新颖的箱式结构,是目前国内中型高压电机的主导产品,以后又随着我国电网电压由6KV升高到10KV,又研发了10KV系列中小型高压异步电动机。
1996年以电科所为首组织有关厂家完成了Y2系列的开发,功率范围为0.12~315KW,机座中心高为63~355。该系列产品显著降低了空载噪声,有效抑制了负载噪声。
2003年电科所组织有关厂家又完整地建立了全系列采用冷轧硅钢片的Y3系列,其能耗达到国标GB18163-2002中能耗限定值的规定,同时也达到欧洲eff2效率标准,并且主要性能指标达到国际同类产品的先进水平。
发展趋势
a 进一步推广高效率异步电动机
1992年美国能源部发布了新的能源法规,提出了高效率三相异步电动机的效率标准(即EPACT指标),并规定从1997年10月24日开始,凡制造和进口一般用途电动机效率必须符合这一标准。以后又更进一步提出超高效率电机(NEMAPremium)。1999年欧洲电机和电力电子制造商协会(CEMEP)制定了eff1、eff2、eff3三个等级的效率标准,并决定到2003年削减50%低于eff3标准水平的电机生产,2006年以后不再生产。
我国也于2002年8月正式实施《中小型三相异步电动机能效限定值及节能评定值》的国标(GB18163-2002)。因此借着节能的规划和“以冷代热”的法令,应该大力推广Y3新系列,使之成为我国低压三相异步电动机的主导产品,且新一轮的派生系列产品也应在Y3新系列上展开。
b 进一步推广变频器供电的三相异步电动机系列的研发与应用
近年来,国民经济各部门对风机和水泵需求不断增长,据有关部门统计,全国风机、水泵电动机装机总容量约35000MW,耗电量约占全国电能耗量的40%左右。以火力发电厂为例,据统计全国火力发电厂的送风机、引风机、一次风机、排粉风机、锅炉给水泵、循环水泵、凝结水泵和灰浆泵等的配套高压电动机总容量约为15000MW,这些设备为长期连续运行但常处于低负荷及变负荷的运行状态,因此其节能潜力很大。据估计通过变频器调速提高风机、水泵系统运行效率的节能潜力每年可达300~500亿度,相当于6~10座装机容量为1000MW级的大型火力发电厂的年发电总量。因此大力推广变频器特别是高压变频器的应用是十分有意义的。目前国际上对高压电动机变频调速技术的研究非常活跃,变频器种类繁多。我国高压电动机多为6KV和10KV等级,由于受到电力电子器件耐压限制,尚难以实现该等级变频器的直接高压输出。而单元串联式多电平变频器的输出电压可达到10KV甚至更高,且输入、输出波形好,对电网的谐波污染小,因此在我国得到广泛应用。国际上该技术比较成熟,输出电压可达14.4KV,变频器采用水冷技术,单机最大容量可达15000KW。我国采用空冷技术,变频器驱动的电动机功率在3500KW以下。
国外变频器基本已做到开环、闭环以及无速度传感器控制三位一体的控制,而我国的产品大多仍是普通的V/F控制方式。业内在变频器调速系统方面已开展了许多研究,当务之急是如何将理论知识转化为工业产品,提高我国变频器的性能和质量。
变频器发展对与之配套的电动机提出了新的要求。以往对配套电动机的研究,主要在减小变频器供电电源的谐波分量所引起的电动机损耗增加、温升升高、振动加大、噪声增大以及谐波转矩增大等方面。近年来,随着IGBT在变频器中的应用,载波频率甚至高达20K,由此带来一系列负面影响,如高频的PWM脉冲波严重影响电动机的绝缘和寿命,变频器输出的共模电压,形成轴电流,造成轴承点蚀,从而缩短电动机寿命。对此电科所及有关厂家已完成了YVF2系列变频专用电机的开发,并完成了《使用纳米技术的新型耐高频脉冲电磁漆线》的项目,该种漆包线耐受高频脉冲能力为普通线的51倍。
此外变频电动机的供电电源经高频调制,其性能测试方法不同于工频电机,急需研制适合变频电机性能测试的方法和检测仪器。
二永磁同步电动机的典型应用与前景
永磁同步电动机发展的条件
(1)高性能低成本的钕铁硼永磁材料具有剩余磁感应强度、矫顽力和磁能积均高的特点,自上世纪80年代以来,又成功解决了钕铁硼材料的热稳定性和耐腐蚀问题,因此用于同步电动机可省去激磁绕组,因无激磁损耗,从而降低了功耗、发热,提高了电机效率和功率因数;由于无需集电环和炭刷,也简化了结构,提高了可靠性。
(2)电力电子器件和技术的进步,发展了各种高性能变频器和专用变频器,解决了同步电动机无法自起动问题,使复杂的阻尼导条和端环得以取消。
(3)易于实现磁场定向控制的矢量变换控制,使永磁同步电动机具有和直流电动机一样优良的线性转矩控制特性。
(4)DSP快速数字信号处理器和各种高性能专用伺服驱动器为各种复杂系统的实现提供了技术基础。
永磁同步电动机发展的机遇
(1)更高的综合节能效果
永磁同步电动机由永磁体激磁,无需励磁电流,故可显著提高功率因数(可达1甚至容性);定子电流小,定子铜耗显著减小;转子无铜耗(三相异步电动机转子绕组损耗约占总损耗的20~30%),因而发热低,可以取消风扇或减小风扇,从而无风摩耗或减少风摩耗,故永磁同步电动机一般比同规格异步电动机效率可提高2~8%,并且在很宽的负载变动范围内始终保持高的效率和功率因数,尤其在轻载运行时节能效果更显著。
(2)可满足某些工业应用需大的起动转矩和最大转矩倍数的动态需求
常规异步电动机起动转矩倍数和最大转矩倍数都有限,为达要求,需选择更大容量的异步电动机,而到了正常运行状态,异步电动机则又处于轻载运行状态,效率和功率因数均较低。例如为油田抽油机设计的具有异步起动能力的永磁同步电动机,起动转矩倍数可达3.6倍以上,效率可达94%,功率因数可达0.95,既满足了负载动态时大转矩的要求,还具有很高的节能效果。
(3)低速直接驱动的需求
为了提高控制精度、减小振动噪声、杜绝油雾带来的不安全,也为了大转矩驱动的需求,近年来对低速电动机的需求也不断增长。如用于电梯拖动的永磁同步曳引机,转矩提高了十几倍,取消了庞大的齿轮箱,通过曳引轮直接拖动轿厢,明显减小了振动和噪声。又如船用吊舱式电力推进器,将低速大转矩的永磁同步电动机置于船舱外的吊舱,无需原来的传动系统,直接驱动螺旋桨,实现船舶的运行和控制。这是船舶驱动技术的又一发展,国外自上世纪九十年代已成功用于豪华邮轮、专用油轮等。西门子公司吊舱式推进器中PMSM容量已达30000KW。
(4)多极高功率因数的需求
近年来,永磁同步电动机朝着多极化发展,多极电机可显著减小定、转子铁心轭部高度,从而减小电机体积、减少铁心用量。多极电机还显著减小了定子端部长度,减小定子铜耗、从而减少发热、提高了效率。如某安装于轿厢和井壁间隙的永磁同步电动机,转子采用60极结构,显著缩短了定子线圈端部长度,实现无机房电梯。若仍用异步电动机驱动,随着极数增加,其功率因数明显降低,在轻载和空载时,功率因数将更低,因此在Y型系列电机中,10极电机已不多见。而该60极永磁同步电动机功率因数高达0.98,空载、轻载时甚至可达1,节能效果明显。
(5)高功率密度的需求
舰船、车辆受体积所限,要求电动机要有高功率密度、高转矩密度。永磁同步电动机由于无需激磁绕组,空间结构小,高性能的钕铁硼永磁材料具有高剩余磁感应强度和高矫顽力,从而可提供很高的磁负荷Bδ,使电机尺寸缩小。有些并联供磁的电机,Bδ甚至可高达1特斯拉以上。传统电机的齿槽结构,约束着磁负荷和电负荷的关系,过高的磁负荷将减小放置绕组的空间,成为实现高功率密度的瓶颈。1986年德国H.Weh教授首先提出横向磁场永磁电机(TransverseFluxPMMachine-TFM)的设想,该设想一反传统结构,使电机的磁负荷和电负荷不再相互制约,特别适合高功率密度、大转矩、低速和直接驱动的场合。横向永磁电机我国目前还处于实验研究阶段。英国研制的用于舰艇的横向磁场电机,功率达10MW,转速为180r/min。此外横向磁场电机在风力发电和海洋潮汐发电中也有应用。
(6)运动控制系统的需求
目前电气传动技术已从简单的速度控制发展到运动轨迹控制。由于永磁同步电动机比异步电动机更易于实现磁场定向矢量变换控制,因此近年来永磁同步伺服电动机系统成了高精度数控机床、机器人等高科技设备的主流。在某些场合,甚至实现了100000∶1的调速范围和小于1~2%的低速转矩波动。外国产品几乎占据了国内所有市场,功率一般为20W~15KW。我国交流伺服电动机和驱动器,尚处在发展初期。
此外机械加工设备的更新,需要各种永磁同步电动机,日本已推出0.75KW~500KW的中小型永磁同步电动机系列,适应各种驱动的要求。
随着对机械加工技术的高速和超高速化、精密和超精密化的需求,具有高速反应能力的直线驱动伺服技术─所谓零传动方式应运而生。由于消除了传统机械传动链所具有的一系列不良影响,因而极大地提高了进给系统的快速反应能力和运动精度,成为新一代数控机床中最具代表性的先进技术之一。目前国外采用直线电机的伺服系统可达到小于0.01μm/min或高达300m/min的运行速度,速度偏差优于±0.01%。如西门子公司的永磁式直线同步电动机最大移动速度为200m/min,最大推力达6600N,最大位移为504mm,应用于高速铣床、曲柄车床、超精密车床等。直线电机伺服系统亦还有着需进一步研究的问题,如直线电动机是直接驱动被控制对象,系统没有任何中间缓冲过程,参数摄动、负载扰动等不确定因素将增加控制难度等。
我国稀土资源丰富,稀土储量为世界其它各国储量的4倍,稀土材料是永磁材料的主要成分,为此充分发挥我国稀土资源的优势,大力开展和推动永磁同步电动机系统的应用和研究,对节能和满足上述各种需求是具有重大战略意义的。
一 中小型异步电动机行业的现状和发展趋势
现状
(1)目前中小型电机产量较高的省市依次为山东、江苏、河北、上海、浙江、广东和辽宁,可见企业大多集中在沿海地区。
(2)由于新兴的民营企业以及合资、外资企业的发展,使中小型电机行业中,国有企业的比重下降,而且中小型电机的产量逐步向“生产大户”集中。
(3)中小型电动机已完整地建立了三相异步电动机Y、Y2、Y3系列。
1985年迅速推广了Y系列及其派生系列产品,其功率范围为0.55~250KW,机座中心高为80~315。 通过引进消化美国西屋公司和瑞士BBC公司的技术,自行研发的Y系列6KV、220~2800KW中型高压三相异步电动机,采用新颖的箱式结构,是目前国内中型高压电机的主导产品,以后又随着我国电网电压由6KV升高到10KV,又研发了10KV系列中小型高压异步电动机。
1996年以电科所为首组织有关厂家完成了Y2系列的开发,功率范围为0.12~315KW,机座中心高为63~355。该系列产品显著降低了空载噪声,有效抑制了负载噪声。
2003年电科所组织有关厂家又完整地建立了全系列采用冷轧硅钢片的Y3系列,其能耗达到国标GB18163-2002中能耗限定值的规定,同时也达到欧洲eff2效率标准,并且主要性能指标达到国际同类产品的先进水平。
发展趋势
a 进一步推广高效率异步电动机
1992年美国能源部发布了新的能源法规,提出了高效率三相异步电动机的效率标准(即EPACT指标),并规定从1997年10月24日开始,凡制造和进口一般用途电动机效率必须符合这一标准。以后又更进一步提出超高效率电机(NEMAPremium)。1999年欧洲电机和电力电子制造商协会(CEMEP)制定了eff1、eff2、eff3三个等级的效率标准,并决定到2003年削减50%低于eff3标准水平的电机生产,2006年以后不再生产。
我国也于2002年8月正式实施《中小型三相异步电动机能效限定值及节能评定值》的国标(GB18163-2002)。因此借着节能的规划和“以冷代热”的法令,应该大力推广Y3新系列,使之成为我国低压三相异步电动机的主导产品,且新一轮的派生系列产品也应在Y3新系列上展开。
b 进一步推广变频器供电的三相异步电动机系列的研发与应用
近年来,国民经济各部门对风机和水泵需求不断增长,据有关部门统计,全国风机、水泵电动机装机总容量约35000MW,耗电量约占全国电能耗量的40%左右。以火力发电厂为例,据统计全国火力发电厂的送风机、引风机、一次风机、排粉风机、锅炉给水泵、循环水泵、凝结水泵和灰浆泵等的配套高压电动机总容量约为15000MW,这些设备为长期连续运行但常处于低负荷及变负荷的运行状态,因此其节能潜力很大。据估计通过变频器调速提高风机、水泵系统运行效率的节能潜力每年可达300~500亿度,相当于6~10座装机容量为1000MW级的大型火力发电厂的年发电总量。因此大力推广变频器特别是高压变频器的应用是十分有意义的。目前国际上对高压电动机变频调速技术的研究非常活跃,变频器种类繁多。我国高压电动机多为6KV和10KV等级,由于受到电力电子器件耐压限制,尚难以实现该等级变频器的直接高压输出。而单元串联式多电平变频器的输出电压可达到10KV甚至更高,且输入、输出波形好,对电网的谐波污染小,因此在我国得到广泛应用。国际上该技术比较成熟,输出电压可达14.4KV,变频器采用水冷技术,单机最大容量可达15000KW。我国采用空冷技术,变频器驱动的电动机功率在3500KW以下。
国外变频器基本已做到开环、闭环以及无速度传感器控制三位一体的控制,而我国的产品大多仍是普通的V/F控制方式。业内在变频器调速系统方面已开展了许多研究,当务之急是如何将理论知识转化为工业产品,提高我国变频器的性能和质量。
变频器发展对与之配套的电动机提出了新的要求。以往对配套电动机的研究,主要在减小变频器供电电源的谐波分量所引起的电动机损耗增加、温升升高、振动加大、噪声增大以及谐波转矩增大等方面。近年来,随着IGBT在变频器中的应用,载波频率甚至高达20K,由此带来一系列负面影响,如高频的PWM脉冲波严重影响电动机的绝缘和寿命,变频器输出的共模电压,形成轴电流,造成轴承点蚀,从而缩短电动机寿命。对此电科所及有关厂家已完成了YVF2系列变频专用电机的开发,并完成了《使用纳米技术的新型耐高频脉冲电磁漆线》的项目,该种漆包线耐受高频脉冲能力为普通线的51倍。
此外变频电动机的供电电源经高频调制,其性能测试方法不同于工频电机,急需研制适合变频电机性能测试的方法和检测仪器。
二永磁同步电动机的典型应用与前景
永磁同步电动机发展的条件
(1)高性能低成本的钕铁硼永磁材料具有剩余磁感应强度、矫顽力和磁能积均高的特点,自上世纪80年代以来,又成功解决了钕铁硼材料的热稳定性和耐腐蚀问题,因此用于同步电动机可省去激磁绕组,因无激磁损耗,从而降低了功耗、发热,提高了电机效率和功率因数;由于无需集电环和炭刷,也简化了结构,提高了可靠性。
(2)电力电子器件和技术的进步,发展了各种高性能变频器和专用变频器,解决了同步电动机无法自起动问题,使复杂的阻尼导条和端环得以取消。
(3)易于实现磁场定向控制的矢量变换控制,使永磁同步电动机具有和直流电动机一样优良的线性转矩控制特性。
(4)DSP快速数字信号处理器和各种高性能专用伺服驱动器为各种复杂系统的实现提供了技术基础。
永磁同步电动机发展的机遇
(1)更高的综合节能效果
永磁同步电动机由永磁体激磁,无需励磁电流,故可显著提高功率因数(可达1甚至容性);定子电流小,定子铜耗显著减小;转子无铜耗(三相异步电动机转子绕组损耗约占总损耗的20~30%),因而发热低,可以取消风扇或减小风扇,从而无风摩耗或减少风摩耗,故永磁同步电动机一般比同规格异步电动机效率可提高2~8%,并且在很宽的负载变动范围内始终保持高的效率和功率因数,尤其在轻载运行时节能效果更显著。
(2)可满足某些工业应用需大的起动转矩和最大转矩倍数的动态需求
常规异步电动机起动转矩倍数和最大转矩倍数都有限,为达要求,需选择更大容量的异步电动机,而到了正常运行状态,异步电动机则又处于轻载运行状态,效率和功率因数均较低。例如为油田抽油机设计的具有异步起动能力的永磁同步电动机,起动转矩倍数可达3.6倍以上,效率可达94%,功率因数可达0.95,既满足了负载动态时大转矩的要求,还具有很高的节能效果。
(3)低速直接驱动的需求
为了提高控制精度、减小振动噪声、杜绝油雾带来的不安全,也为了大转矩驱动的需求,近年来对低速电动机的需求也不断增长。如用于电梯拖动的永磁同步曳引机,转矩提高了十几倍,取消了庞大的齿轮箱,通过曳引轮直接拖动轿厢,明显减小了振动和噪声。又如船用吊舱式电力推进器,将低速大转矩的永磁同步电动机置于船舱外的吊舱,无需原来的传动系统,直接驱动螺旋桨,实现船舶的运行和控制。这是船舶驱动技术的又一发展,国外自上世纪九十年代已成功用于豪华邮轮、专用油轮等。西门子公司吊舱式推进器中PMSM容量已达30000KW。
(4)多极高功率因数的需求
近年来,永磁同步电动机朝着多极化发展,多极电机可显著减小定、转子铁心轭部高度,从而减小电机体积、减少铁心用量。多极电机还显著减小了定子端部长度,减小定子铜耗、从而减少发热、提高了效率。如某安装于轿厢和井壁间隙的永磁同步电动机,转子采用60极结构,显著缩短了定子线圈端部长度,实现无机房电梯。若仍用异步电动机驱动,随着极数增加,其功率因数明显降低,在轻载和空载时,功率因数将更低,因此在Y型系列电机中,10极电机已不多见。而该60极永磁同步电动机功率因数高达0.98,空载、轻载时甚至可达1,节能效果明显。
(5)高功率密度的需求
舰船、车辆受体积所限,要求电动机要有高功率密度、高转矩密度。永磁同步电动机由于无需激磁绕组,空间结构小,高性能的钕铁硼永磁材料具有高剩余磁感应强度和高矫顽力,从而可提供很高的磁负荷Bδ,使电机尺寸缩小。有些并联供磁的电机,Bδ甚至可高达1特斯拉以上。传统电机的齿槽结构,约束着磁负荷和电负荷的关系,过高的磁负荷将减小放置绕组的空间,成为实现高功率密度的瓶颈。1986年德国H.Weh教授首先提出横向磁场永磁电机(TransverseFluxPMMachine-TFM)的设想,该设想一反传统结构,使电机的磁负荷和电负荷不再相互制约,特别适合高功率密度、大转矩、低速和直接驱动的场合。横向永磁电机我国目前还处于实验研究阶段。英国研制的用于舰艇的横向磁场电机,功率达10MW,转速为180r/min。此外横向磁场电机在风力发电和海洋潮汐发电中也有应用。
(6)运动控制系统的需求
目前电气传动技术已从简单的速度控制发展到运动轨迹控制。由于永磁同步电动机比异步电动机更易于实现磁场定向矢量变换控制,因此近年来永磁同步伺服电动机系统成了高精度数控机床、机器人等高科技设备的主流。在某些场合,甚至实现了100000∶1的调速范围和小于1~2%的低速转矩波动。外国产品几乎占据了国内所有市场,功率一般为20W~15KW。我国交流伺服电动机和驱动器,尚处在发展初期。
此外机械加工设备的更新,需要各种永磁同步电动机,日本已推出0.75KW~500KW的中小型永磁同步电动机系列,适应各种驱动的要求。
随着对机械加工技术的高速和超高速化、精密和超精密化的需求,具有高速反应能力的直线驱动伺服技术─所谓零传动方式应运而生。由于消除了传统机械传动链所具有的一系列不良影响,因而极大地提高了进给系统的快速反应能力和运动精度,成为新一代数控机床中最具代表性的先进技术之一。目前国外采用直线电机的伺服系统可达到小于0.01μm/min或高达300m/min的运行速度,速度偏差优于±0.01%。如西门子公司的永磁式直线同步电动机最大移动速度为200m/min,最大推力达6600N,最大位移为504mm,应用于高速铣床、曲柄车床、超精密车床等。直线电机伺服系统亦还有着需进一步研究的问题,如直线电动机是直接驱动被控制对象,系统没有任何中间缓冲过程,参数摄动、负载扰动等不确定因素将增加控制难度等。
我国稀土资源丰富,稀土储量为世界其它各国储量的4倍,稀土材料是永磁材料的主要成分,为此充分发挥我国稀土资源的优势,大力开展和推动永磁同步电动机系统的应用和研究,对节能和满足上述各种需求是具有重大战略意义的。
免责声明:本文仅代表作者个人观点,与电源在线网无关。其原创性以及文中陈述文字和内容未经本站证实,对本文以及其中全部或者部分内容、文字的真实性、完整性、及时性本站不作任何保证或承诺,请读者仅作参考,并请自行核实相关内容。
编辑:Sepnova
编辑:Sepnova
本文链接:节能给电机行业带来的机遇
http:www.cps800.com/news/2006-12/20061230113942.html
http:www.cps800.com/news/2006-12/20061230113942.html
文章标签: 电源/电机/节能

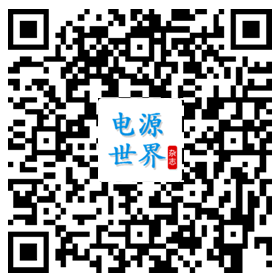