可充电锂离子二次电池具有高比能量、长循环寿命、无记忆效应的特性,又具有安全、可靠且能快速充放电等优点,因而成为近年来新型电源技术研究的热点。由于锂离子电池是绿色环保型无污染的二次电池,符合当今各国能源环保方面大的发展需求,在各行各业的使用量正在迅速增加。目前二次锂离子电池除广泛用于日常熟知的手机、笔记本电脑以及MP3等数码电子产品外,近年在电动车、电动自行车等一些大功率电池方面也已经开始使用。从2001年起,全球锂离子电池产量以每年40%的速度在迅速递增。根据爱尔兰ResearchandMarkets近日发布了锂电池的市场预测表示,目前包括中国大陆、香港、中国台湾地区在内,中国锂电池产量为全球最大规模。在全球锂电池总产量中,中国大陆占16.9%,中国台湾地区占6.9%。中国化学与物理电源行业协会表示,2006年中国大陆的锂充电电池产量为9.5亿个。2007年预计将达到10亿个,比上年增加11%。该协会还预测,几乎所有厂商都将在今后两年内把产量最多提高50%。
一、锂离子电池隔膜市场分析
通常的锂离子二次电池由正/负极材料、电解液、隔膜以及电池外壳包装材料组成。隔膜是液态锂离子二次电池的重要组成部分,在电池中起着防止正/负极短路,同时在充放电过程中提供离子运输电通道的作用,其性能决定了电池的界面结构、内阻等,直接影响电池的容量、循环性能以及安全性能等特性,性能优异的隔膜对提高电池的综合性能具有重要的作用。锂离子电池隔膜的材料主要有聚丙烯(PP)、聚乙烯(PE)单层微孔膜,以及由PP和PE复合的多层微孔膜。目前,世界上只有日本、美国等少数几个国家拥有锂离子电池聚合物隔膜的生产技术和相应的规模化产业。我国在锂离子电池隔膜的研究与开发方面起步较晚,锂离子电池隔膜主要仍然依赖进口,导致市场价格高居不下,隔膜的平均价格在8~15元/m2,其成本占到了整个电池成本的约1/3。按照电池产量10亿只估计,每年隔膜的消耗量在3亿~5亿m2之间,市场价值在10~15亿元。目前国内隔膜市场80%以上被美、日进口产品占领,国产隔膜主要在中、低端市场使用。所以实现隔膜的国产化,生产优质的国产化隔膜,一方面有望能够降低整个隔膜的市场价格,同时还能为国家节省大量外汇,创造巨大的经济效益。
二、锂离子电池隔膜国产化进展
目前市场化的锂离子电池隔膜主要聚乙烯、聚丙烯为主的聚烯烃隔膜,包括单层PE,单层PP,三层PP/PE/PP复合膜。现有的聚烯烃隔膜生产工艺可按照干法和湿法分为两大类,同时干法又可细分为单向拉伸工艺和双向拉伸工艺。
干法单向拉伸工艺是通过生产硬弹性纤维的方法,制备出低结晶度的高取向聚丙烯或聚乙烯薄膜,在高温退火获得高结晶度的取向薄膜。这种薄膜先在低温下进行拉伸形成银纹等微缺陷,然后高温下使缺陷拉开,形成微孔。这种方法最早见于美国Celanse公司1970年专利USPatent3426754,用于生产单层的聚丙烯多孔膜。该工艺经过几十年的发展在美国、日本已经非常成熟,现在美国Celgard公司、日本UBE公司采用此种工艺生产单层PP、PE以及三层PP/PE/PP复合膜。用这种方法生产的隔膜具有扁长的微孔结构,由于只进行单向拉伸,隔膜的横向强度比较差,但正是由于没有进行横向拉伸,横向几乎没有热收缩。
由于受国外专利保护及知识产权方面的制约,国内采用单向拉伸方法制备隔膜的工业化进展很慢。国内2004年已经开始有这方面工艺的专利,和国外专利的不同之处在于,在聚丙烯中加入具有结晶促进作用的成核剂以及油类添加剂剂,加速了退火过程中的结晶速率。该技术现用于杭州一条生产线,采用单向拉伸的方法进行PP单层隔膜的生产,已经有此种类型的国产隔膜在市场上销售。
湿法又称相分离法或热致相分离法,将高沸点小分子作为致孔剂添加到聚烯烃中,加热熔融成均匀体系,然后降温发生相分离,拉伸后用有机溶剂萃取出小分子,可制备出相互贯通的微孔膜材料,适用的材料广。采用该法的具有代表性的公司有日本旭化成、东燃及美国Entek等,目前主要用于单层的PE隔膜。用湿法双向拉伸方法生产的隔膜由于经过了双向拉伸具有较高的纵向和横向强度。国内佛山塑料集团在2004年建立了一条采用湿法工艺生产PE隔膜的双向拉伸生产线,2005年底开始有产品在市场上销售。
干法双向拉伸工艺是中国科学院化学研究所在20世纪90年代初开发出的具有自主知识产权的工艺(CN1062357)。通过在聚丙烯中加入具有成核作用的β晶型改进剂,利用聚丙烯不同相态间密度的差异,在拉伸过程中发生晶型转变形成微孔,用于生产单层PP膜。从2000年开始,在国家863计划项目的支持下,具有自主知识产权的干法双向拉伸制备聚丙烯微孔膜的技术在营口向阳化工厂进行中试。由于资金的匮乏,中试采用拉伸双轴取向聚丙烯的设备,制备聚丙烯微孔膜所需要的工艺条件无法很好地在该设备上实现,虽然在中试过程实现了小批量生产,但膜的性能无法满足锂电池厂对隔膜性能的要求。从2005年开始,中国科学院化学研究所与新时科技公司合作重新开展干法双向拉伸工艺的中试研究。根据中试工作取得的经验,于2007年11月成功建成并投产了一条年产聚丙烯微孔膜600万m2的生产线。用此工艺生产的聚丙烯微孔膜具有不同于以上工艺制得隔膜的微孔结构。通过国内30多家电池厂在锂离子电池上进行评价,产品基本性能已经完全满足锂离子电池隔膜的质量指标要求,市场反应积极,2008年2月份开始已经有产品在市场上销售。目前公司正通过建立、健全企业管理制度,完善质量管理体系进一步提高产品质量水平。同时采用干法双向拉伸工艺的还有河南新乡一家公司,于2004年进行中试及生产,2005年底开始有产品在市场上销售。同期开始筹备新的生产线,于2007年正式投产,现有年生产能力约为1500万m2。该公司大部分产品满足国内低、中端市场需求,少部分产品已经能够满足高端市场的质量要求。由于该公司采用的工艺及配方是通过非正常手段从中国科学院化学研究所获取,有可能面临知识产权方面的困扰,现在中国科学院化学研究所正采取措施,寻求法律解决。
纵观国内的锂离子电池隔膜市场,虽然目前依然是国外品牌一统天下,但是隔膜的国产化已经呈现出喜人的局面。现在国内3种类型的聚烯烃隔膜均已经实现了市场化,并且产能在逐步扩大,产品的质量也在不断提升。目前国产隔膜在低、中端市场已经大部分替代了进口产品,少量产品已经进入高端市场,市场价格随着国产隔膜的问世已经有所降低,由2003年的15~20元/m2降低到现在的8~15元/m2。
三、锂离子电池隔膜的未来发展趋势
电池隔膜的发展是随着锂离子电池的需求不断变化而不断发展的,从体积上看,锂离子电池正在朝着小和大两个截然不同的方向发展。
在一些如手机、数码相机等电子产品上,为了迎合美观、便于携带的需求,电池厂将电池的电芯做得非常小巧。为了追求高的能量密度,在狭小的体积中能容纳下更多的电极材料,电池厂家希望隔膜的厚度越薄越好,通常隔膜的厚度为25μm,现在很多厂家要求提供20μm甚至16μm厚的隔膜。隔膜的性能影响离子电导率,从而直接影响电池的容量、循环性能以及安全性能等性能。由于聚乙烯、聚丙烯等聚烯烃非极性材料制成的隔膜具有低的表面能,在锂离子电池使用的极性碳酸酯类电解液中虽能很好的浸润,但由于吸液性能并不太好,离子电导率低。材料的表面性能可以通过表面处理进行改善,离子辐照、表面等离子体处理以及紫外光照射接枝等方法已经是非常成熟的表面处理方法。对聚烯烃隔膜进行表面处理,提高隔膜的吸液性能,将是提高隔膜性能的一个重要方向。
而与此相反,在电动自行车、电动汽车及电动工具等所使用的动力电池方面,为了获得高的容量、提供大的功率,通常一个电池需要使用几十甚至上百个电芯进行串接。由于锂电池具有潜在的爆炸危险,隔膜的安全性相当重要,现在市场上对厚度为40μm聚丙烯隔膜的需求量在日益增加。但无论聚乙烯、聚丙烯还是其他热塑性高分子材料,在接近熔点时材料均会因熔化而收缩变形,给动力电池的安全性带来潜在的隐患。无机物如氧化铝、氧化锆等在100~300℃的范围内非常稳定,且它们的微/纳米材料已经市场化。德国的Degussa公司结合有机物的柔性和无机物良好热稳定性的特点,提出一种在无纺布表面复合无机陶瓷氧化物涂层的方法,制备出了有机底膜/无机涂层复合的锂离子电池隔膜。在电池充放电过程中,即使有机底膜发生熔化,无机涂层仍然能够保持隔膜的完整性,防止大面积正/负极短路现象的出现,这种有机/无机复合的隔膜为解决大功率的电池安全性提供了一个可行的解决方案,将是国内未来锂离子动力电池隔膜的一个重要发展方向。
编辑:coco
来源:中国电子元件行业协会
http:www.cps800.com/news/2008-4/20084911534.html

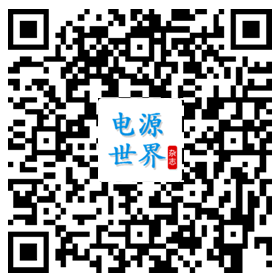